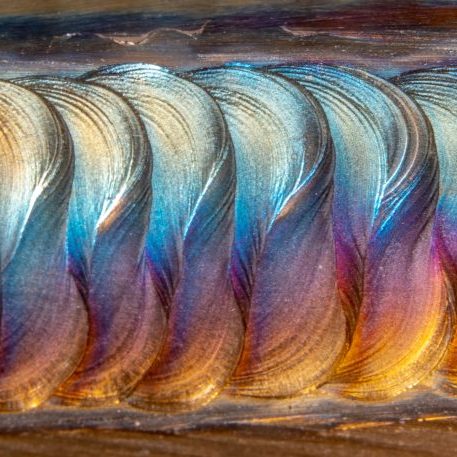
TIG Welding Thin-Wall Tubing: 304 Stainless Steel
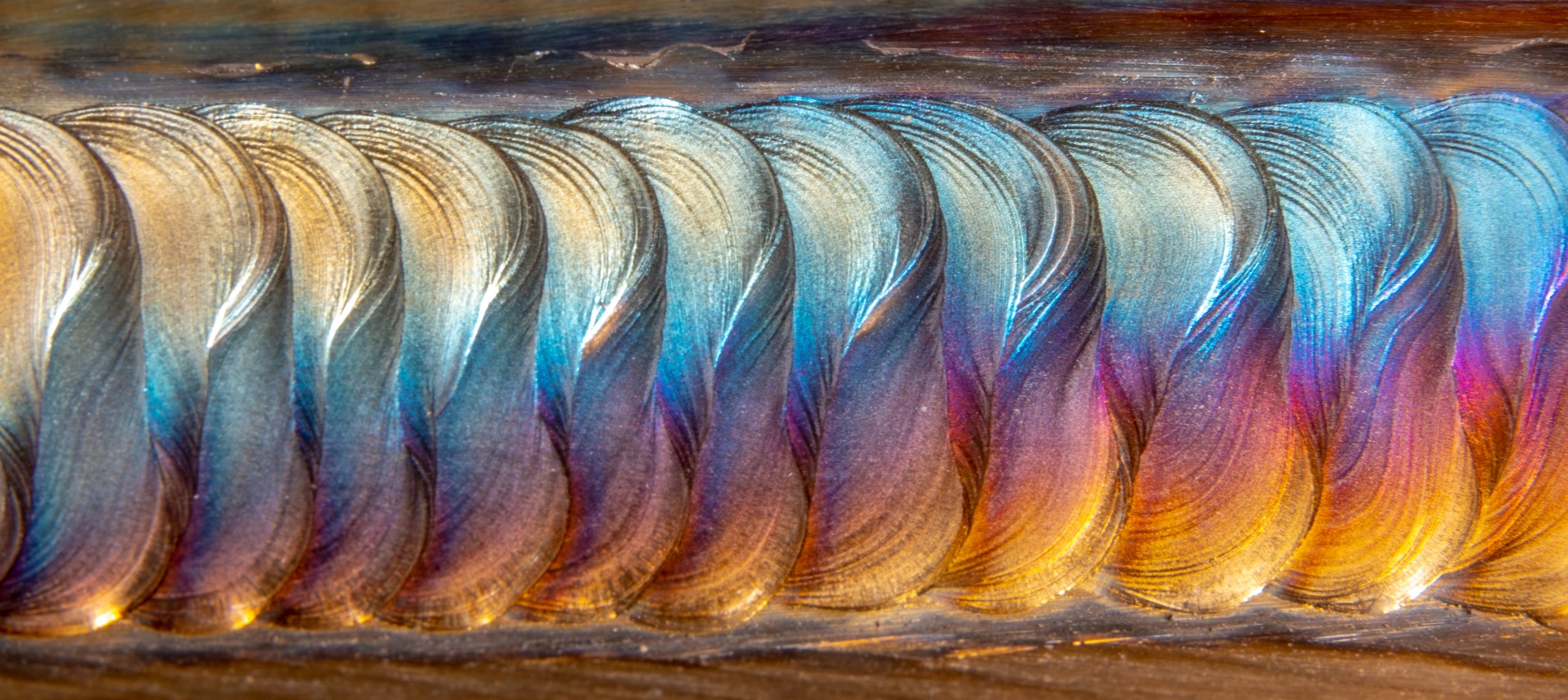
TIG welding (Tungsten Inert Gas welding) is the preferred method for joining thin-wall tubing made of 304 stainless steel due to its precision and ability to create clean, high-quality welds. This process is particularly suitable for applications where aesthetics and structural integrity are critical, such as aerospace, automotive, and food-grade industries. Below are key considerations and tips for TIG welding thin-wall 304 stainless steel tubing effectively.
Preparation is Key
- Cleanliness: Thoroughly clean the tubing to remove oils, dirt, and oxidation. Use a stainless steel wire brush and acetone to prepare the surface.
- Fit-Up: Ensure the tubing is well-aligned with tight and consistent gaps. Loose fit-ups can lead to uneven penetration and warping.
- Edge Preparation: For extremely thin walls (e.g., <1mm), ensure the edges are smooth and burr-free to prevent burn-through.
Equipment Setup
- Electrode: Use a 2% thoriated or ceriated tungsten electrode, typically sharpened at a 45° angle to a fine point for precise arc control.
- Shielding Gas: Argon is the most common shielding gas. Use a 10-20 CFH flow rate to prevent oxidation and maintain a clean weld. You may have to increase your CFH flow rate when using larger-sized cups.
- Filler Rod: For optimal compatibility, select a filler rod that matches the base material, such as ER308L.
Welding Parameters
- Low Amperage: Use a low amperage setting to avoid overheating and burn-through. Start around 20-50 amps, depending on the tubing thickness.
- Pulse Welding: If your TIG welder has a pulse feature, use it to control heat input. Pulse welding is beneficial for thin materials.
- Travel Speed: Maintain a consistent and relatively quick speed to minimize heat buildup.
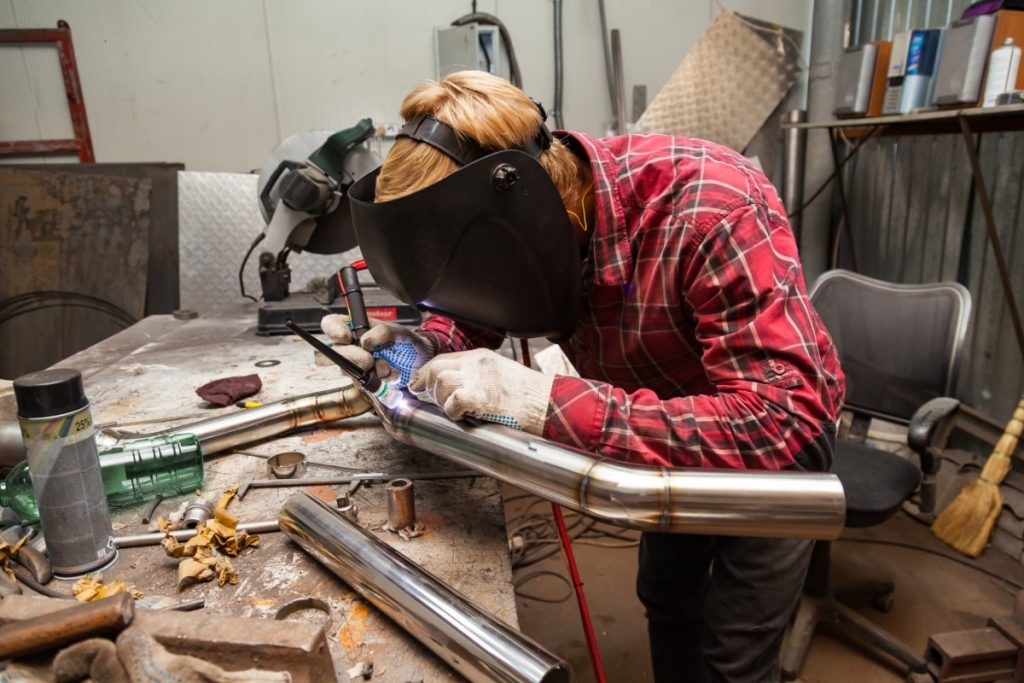
Technique
- Tack Welding: Begin with tack welds around the tubing to hold it in place. Tacking reduces distortion and ensures even heat distribution.
- Steady Hand: Use a steady hand and maintain a tight arc length—ideally no more than 1-2 mm.
- Back Purging: For thin-wall tubing, back purging with argon is essential to prevent oxidation on the inside of the weld.
Common Challenges and Solutions
- Warping: Use a heat sink or fixture to reduce distortion.
- Burn-Through: Lower the amperage or increase travel speed if burn-through occurs.
- Oxidation: Ensure sufficient shielding gas coverage and avoid drafts in the work area.
Conclusion
TIG welding thin-wall 304 stainless steel tubing demands precision and attention to detail. You can achieve strong, aesthetically pleasing welds by focusing on proper preparation, equipment setup, and technique. Even challenging thin-wall applications can be mastered with practice and attention to the key factors outlined above.
Why Choose Haze Performance?
Engineered for quality, Haze is the ultimate hub for providing aftermarket parts for car enthusiasts to upgrade their vehicles.
Haze specializes in producing top-grade stainless steel exhaust systems with all the necessary features to create a better driving experience. Work on your exhaust system with a range of high-quality products from a team of automotive and racing enthusiasts.
We’re committed to sourcing only premium-grade materials that guarantee superior results with every exhaust system upgrade we make — because there’s no room for compromise regarding performance. Discover the Haze difference now!